Manufacturing and engineering
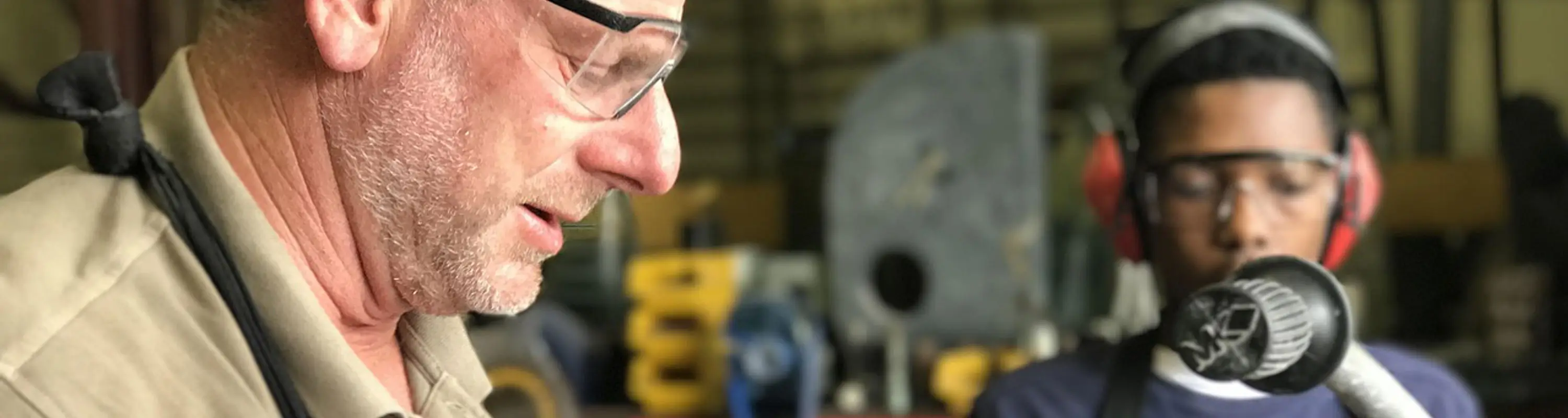
Almost every object has been manufactured in some way, whether in a factory by huge machines or with hand tools in a small workshop.
Manufacturing and engineering apprenticeship programmes are designed to train and mentor highly skilled staff for careers requiring precision skills.
Find out about our apprenticeships using the drop down buttons below. These include information about entry requirements, course content and next steps.
Who is this Apprenticeship for?
This course is for any eligible candidates, who wish to earn a wage while developing their skills and knowledge needed to be able to pursue a career in wood manufacturing.
Wood product manufacturing is at the engineering end of woodworking and forms a critical part of the emerging pre-manufactured solutions sector, identified in the Farmer Review as key to the future of construction. It supplies products to the housing, commercial, public and building sectors. Employers range from small to large, with a prevalence in the medium to large end of the market. Specialism in single product type is particularly common in the larger end of the market. The broad purpose of the occupation is to produce high volume, repetitive, engineered products from timber. Presenting a wide and varied specification for both external and interior applications, products such as roofing components, windows, doors, door-sets, staircases and other timber construction items.
As well as utilising traditional materials, they use engineered and modified timbers to support product design and delivery. They cut, layout and assemble materials, working to a specification. Depending on the product, they may install fixtures and fittings, apply finishes and add glazing systems.
Wood product manufacturing operatives typically work individually but can also form part of a larger production team and will report to the production supervisor/manager. Workplaces can be wide ranging from small workshops to large state of the art manufacturing facilities. In their daily work, an employee in this occupation interacts with customers, delivery personnel, design office, internal stores and suppliers, depending on the size of the organisation. An employee in this occupation will be responsible for completing their own work to specification, with minimal supervision, ensuring they meet set deadlines. They are responsible for meeting quality requirements and working in accordance with health and safety and environmental considerations.
Are there any entry requirements?
Must be a UK citizen, or have the right of abode in the UK, or is a citizen of a country that is within the EEA and have been ordinarily resident in the UK, the EU or the EEA continuously for the previous three years before the start of learning.
Candidates aged 16-18 will have achieved a minimum of GCSE Grade 1 (G) or equivalent Level 1 in English and Mathematics. We also offer Functional Skills English and maths at Level 1 and Level 2 for those needing to gain these qualifications prior to enrolment.
Apprentices must be employed, normally for a minimum of 30 hours, in a role that suits the skills requirements of this apprenticeship. If you are not already employed, in this type of job role, you could search our apprenticeship vacancy page at:
www.darlington.gov.uk/jobs-and-careers/apprenticeships/apprenticeship-vacancies/
New applicants will be contacted by a vocational delivery tutor to determine suitability/ eligibility prior, give information and advice on the next steps.
Shortlisted applicants will be sent to the employer, to then follow their recruitment procedure. Unsuitable applicants will be signed posted to other areas of our service to develop transferable/ employability skills, with a view to ensuring they are suitable for other apprenticeship positions in the future.
What is the curriculum intent of this Apprenticeship?
The structure and delivery of the course curriculum will enable you to develop the skills, knowledge and behaviours to reflect the needs of local and regional employers, gain qualifications and be successful in this area.
The curriculum is planned and sequenced to enable learners with previous knowledge and experience to develop the new skills needed to progress to the next stage of their career, training, education or employment. The curriculum is flexible and responsive to learner demands and can be tailored to suit individual needs, arising from any current and dynamic issues affecting their role, which can be addressed during workshop sessions.
As an apprentice you will need to be able to demonstrate knowledge and practical skills at the end of your apprenticeship training programme and understand how this reflects the needs of the local, regional and national economy.
What will the Apprenticeship cover?
The Wood Product Manufacturing Operative Level 2 Apprenticeship will develop the knowledge and understanding of:
- Health and Safety
- Environmental and sustainability considerations, regulations and good practice.
- How different products are expected to perform, and how they interact with the wider built environment.
- Types of customers
- The wood product manufacturing industry, its background and importance.
- Requirements for glazing wood products
- Quality standards and product accreditation processes for wood product manufacture
- Commercial operations and how they contribute; key functions involved in the wood product manufacturing process.
- Checking and clarifying work requirements, including what needs checking and why.
- Principles and uses of Computer Numerically Controlled (CNC) machinery
- Different materials used to manufacture wood products and components
- Machines, equipment and tools used in wood product manufacturing
- Work and product specifications, what they are and how to use them.
- Different types of adhesives, and processes for their use including application methods.
- Different grit sizes and the sequence of sanding for full finish paint and stain systems.
- Techniques for applying specified finishes to components and products.
- Techniques for installing fixtures and fittings to wood products.
- Assembly methods.
- Types of faults and errors that do occur, investigation and rectification techniques.
- Procedures for the safe handling and storage of wood components, products and glazing systems.
- Documentation requirements; written and verbal communication techniques.
- Processes for handover to other manufacturing process functions.
- Techniques for measuring and cutting components and products.
- Manufacturing processes used to produce the end-product.
Develop the skills in:
- Comply with health, safety and environmental requirements
- Identify risks and hazards in the workplace and apply appropriate control measures.
- Comply with organisational and statutory environmental and sustainability considerations.
- Communication
- Plan work to undertake wood product manufacturing operations.
- Carry out glazing operations.
- Read and interpret specifications, diagrams and work instructions, and following these instructions.
- Prepare the work area before undertaking the work.
- Position wood components and apply manual and mechanical cramps to ensure products are secured and in accordance with the work specification.
- Prepare and operate Computer Numerically Controlled (CNC) equipment.
- Select the correct type and quantity of components and materials.
- Select, set up and operate machinery, tools and equipment used to produce wood components.
- Use and maintain jigs and templates for wood product manufacturing operations.
- Apply adhesives to wood components.
- Sand materials and de-nib.
- Apply finishes to wood products.
- Install fixtures and fittings to wood products.
- Assemble wood components to the work specification and given tolerances.
- Identify faults and issues.
- Report work outcomes and/or problems.
- Complete work documentation.
- Complete the handover process to other manufacturing process functions/teams.
- Check and inspect work to ensure it meets the work specification; undertake rectification or rework where necessary.
- Pack and store products and components.
Develop the behaviours in:
- Safety first attitude
- Adaptable
- Collaborates with others
- Pride in the workplace
- Self-motivated
- Quality workmanship
On completion of the on-programme element of the apprenticeship you will enter gateway to the End Point Assessment, which is the final assessment. This will be conducted by an independent end point assessor who will grade the assessment.
End Point Assessment Methods
To trigger the End Point Assessment, you must have:
- Proof of English & maths GCSE minimum grade 1 (G) or equivalent level 1 qualification
- Completed a showcase portfolio, demonstrating how you have met the knowledge, skills and behaviours
The End Point Assessment consists of:
- Workplace Observation: A pre-planned observation with questions, in your normal place of work and independently assessed. The observation will be for 3 hours, in total.
- Knowledge Test: An online multiple-choice test, consisting of 30 questions over a 60-minute duration
- Professional Discussion: A 45-minute structured discussion, underpinned by a portfolio of evidence, with the Independent Assessor. This is to draw out the best of the apprentice’s competence and excellence and cover the knowledge, skills and behaviours
This standard will be graded as Distinction, Merit, Pass or Fail.
What could I do when I have finished this Apprenticeship?
This apprenticeship provides an ideal entry into the occupation and supports progression within the sector as a CNC (computer numerically controlled) operative, Finishing operative/sprayer and assembler or Machinist.
You may gain employment with your employer but will also be given information and guidance to continue onto other courses.
Where and when will I learn?
During the course you will be expected to attend work a minimum of 30 hours per week where you will learn the skills and knowledge required to continue through your qualification. You will be supported in the workplace through regular visits with your tutor and may be needed to come into one of our training centres (Lingfield Way, DL1 4QZ or Coleridge Centre, DL1 5AJ) for support sessions. These sessions will allow you to complete coursework, receive instant feedback and ensure you are ready for the End Point Assessment.
This course will typically take 24 months, but this is based on a vocational initial assessment to determine prior learning in this area and may be reduced.
How much will the Apprenticeship cost?
There are no fees for this apprenticeship.
What do I do next?
You can:
Or you can:
- Apply for this apprenticeship area [external link] to be entered into a 'pool of candidates'. When a relevant vacancy becomes available we will contact you.
- If you are already employed in this area and wish to join the apprenticeship training, or have identified an employer wishing to start you as an apprentice in this area, please contact us
Who is this course for?
This course is for any eligible candidates, who wish to earn a wage while developing their skills and knowledge needed to be able to pursue a career in the manufacturing sector.
As a Lean Manufacturing Operative, you will be expected to carry out your work safely and meet the exacting quality standards demanded in a fast paced and efficient processing environment and develop into a multi-skilled operator through process ownership. You could be required to carry out manufacturing activities on multiple products with different specifications consecutively e.g. automotive manufacturing – Multi models manufacturing results in the manufacturing of different models of vehicle with different specification variants within a high-volume environment.
You will be required to prepare, control, contribute to and complete manufacturing operations, and follow manufacturing processes and standard operating procedures whilst adhering to specific safe working policies & procedures. You would work closely with stakeholders and will have clear reporting lines to ensure appropriate escalation.
Examples of the job titles from across the manufacturing sector that would be covered within this standard are:
Team Member Production; Manufacturing Production Operative; Manufacturing Assembly Operative; Manufacturing Inspection/Quality Assurance Operative; Manufacturing Logistics Operative; Manufacturing Material Handling Operative; Manufacturing Process/Finishing Operative
A Lean Manufacturing Operative must have the core requirements below and demonstrate the specialist requirements in ONE job specific role, which include:
- Production/Assembly role
- Inspection/Quality assurance role
- Logistics/Material handling role
- Production processing/finishing role
Entry Requirements
Must be a UK citizen, or have the right of abode in the UK, or is a citizen of a country that is within the EEA and have been ordinarily resident in the UK, the EU or the EEA continuously for the previous three years before the start of learning.
Candidates aged 16-18 will have achieved a minimum of GCSE Grade 1 (G) or equivalent Level 1 in English and Mathematics. We also offer Functional Skills English and maths at Level 1 and Level 2 for those needing to gain these qualifications prior to enrolment.
Apprentices must be employed, normally for a minimum of 30 hours, in a role that suits the skills requirements of this apprenticeship. If you are not already employed, in this type of job role, you could search our apprenticeship vacancy page at:
www.darlington.gov.uk/jobs-and-careers/apprenticeships/apprenticeship-vacancies/
New applicants will be contacted by a vocational delivery tutor to determine suitability/ eligibility prior, give information and advice on the next steps.
Shortlisted applicants will be sent to the employer, to then follow their recruitment procedure. Unsuitable applicants will be signed posted to other areas of our service to develop transferable/ employability skills, with a view to ensuring they are suitable for other apprenticeship positions in the future.
What is the curriculum intent of this apprenticeship?
The structure and delivery of the course curriculum will enable you to develop the skills, knowledge and behaviours to reflect the needs of local and regional employers, gain qualifications and be successful in this area.
The curriculum is planned and sequenced to enable learners with previous knowledge and experience to develop the new skills needed to progress to the next stage of their career, training, education or employment.
The curriculum is flexible and responsive to learner demands and can be tailored to suit individual needs, arising from any current and dynamic issues affecting their role, which can be addressed during workshop sessions.
As an apprentice you will need to be able to demonstrate knowledge and practical skills at the end of your apprenticeship training programme and understand how this reflects the needs of the local, regional and national economy.
What will the apprenticeship cover?
The Lean Manufacturing Operative Level 2 Apprenticeship will
Develop the knowledge and understanding of:
- Health & Safety: Relevant statutory, organisational and health and safety regulations relating to lean manufacturing operations and safe practices.
- Environmental: Compliance procedures/systems in line with regulatory requirements.
- Production: Their individual roles and responsibilities within the organisation and the flexibility required to deliver products to meet customers costs/delivery targets/requirements.
- Lean Manufacturing Operations: Manufacturing standard operation procedures (SOPs) adherence and development of lean processes
- Quality Control: Process equipment monitoring, data collection, error proofing and operating procedures e.g. ISO 9002 or other relevant quality standards.
- Problem Solving: The tools and methods of effective problem-solving using data, reports, and documents to resolve production related issues e.g. A3 report, graphs, matrices and escalate concerns.
- Continuous Improvement: How to study and identify ways to improve the safety, quality, cost or process efficiency using lean manufacturing tools.
- Communication: How to share information using a range of methods within the manufacturing environment e.g. oral, written, electronic, information boards, visual displays.
- Workplace Organisation: How to maintain a safe and efficient work site through workplace organisation
Please note additional knowledge units will be worked towards, specific to the manufacturing route taken
Develop the skills in:
- Health & Safety: Work safely always, complying with health and safety legislation, regulations, and other relevant guidelines. Identifying risks within their processes and support/carry out countermeasure activities to improve safe working. Manage tooling, equipment, and materials daily in-line with supplier standards.
- Environmental: Comply with environmental procedures and systems and contribute to the achievement of specific standards.
- Production: Demonstrate their ability to carry out their role effectively, efficiently, and flexibly maintaining lean manufacturing principles to meet customer’s demands.
- Lean Manufacturing Operations: Demonstrate their skill and knowledge following SOPs and building their versatility across several processes and process areas. Select and use appropriate tools, equipment, and materials to carry out the manufacturing operation.
- Quality Control: Demonstrate appropriate process documentation control. Accurately completing check sheets, monitoring process and equipment data efficiently and legibly using the correct terminology required to meet the quality standard.
- Problem Solving: Demonstrate their ability to identify and resolve problems within the lean manufacturing environment using effective problem-solving tools and techniques. Manage problems that may occur during the manufacturing process within the limits of their responsibility and escalate as appropriate.
- Continuous Improvement: Generate ideas and contribute to process improvement activities individually or as part of a team through fact finding and analysis to improve the safety, environment, quality, cost, or production process. Identifying and eliminating the 7 wastes (defects, over production, transportation, waiting, inventory, motion and processing).
- Communication: Demonstrate communication skills which include oral, written, electronic (PC), information boards or visual displays to effectively share information.
- Workplace Organisation: Maintains and monitors the work site efficiently and effectively at all times using the elements of sifting, sorting, sweeping, spick & span (5’s) within the lean manufacturing environment.
Please note additional skills units will be worked towards, specific to the manufacturing route taken
Develop and demonstrate the following behaviours:
- Punctual, reliable and takes responsibility for their own actions.
- Show respect for others, having regard for diversity and equality.
- Respond positively to change in the working environment.
- Integrates within the team and supports others.
- Can work independently and effectively in challenging situations.
- Maintains quality of work under pressure.
- An open and honest communicator.
- Listens to other people’s opinions.
- A positive and respectful attitude.
- Follows instructions and guidance and demonstrates attention to detail.
- Seeks opportunities to develop and adapt to different situations, environments or technologies..
On completion of the on-programme element of the apprenticeship you will enter gateway to the End Point Assessment, which is the final assessment. This will be conducted by an independent end point assessor who will grade the assessment.
End Point Assessment methods
To trigger the End Point Assessment, you must:
- Proof of English & maths GCSE minimum grade 1 (G) or equivalent level 1 qualification
- Have completed or have certified proof of Level 2 Diploma in Manufacturing.
- Completed a showcase portfolio, demonstrating how you have met the knowledge, skills and behaviours.
The End Point Assessment consists of:
- Observation of Practice – 120 mins observed in the workplace (this includes Q&A).
- Professional discussion – 40 mins (underpinned with a portfolio of evidence).
This standard will be graded as Distinction, Pass or Fail.
What could I do when I finish my apprenticeship?
You may gain employment with your employer and / or work towards the Team Leader Level 3 Apprenticeship, depending on job role.
You will also be given information and guidance to continue onto other courses.
Where and when will I learn?
During the course you will be expected to, normally, attend work a minimum of 30 hours per week where you will learn the skills and knowledge required to continue through your qualification. This may include shift working, bank holiday working and weekend working. You will be supported in the workplace through regular visits with your tutor and you will also be expected to come into the training centre (Coleridge Centre, DL1 5AJ) for support sessions. These sessions will allow you to complete coursework, receive instant feedback and ensure you are ready for the End Point Assessment
This on-programme taught element will typically take 15 months, but this is based on a vocational initial assessment to determine prior learning in this area and may be reduced. The course duration is based on the apprentice working 30 hours per week but will be extended if the apprentice works less hours. The End Point Assessment will be completed within 3 months of completing the on-programme taught element.
How much will the apprenticeship cost?
There are no costs to the apprentice for this course
What do I do next?
If you are already employed in this area and wish to join the course, or have identified an employer wishing to start you as an apprentice in this area contact us on 01325 405601
Alternatively …
Who is this Apprenticeship for?
This apprenticeship is for any eligible candidates, who wish to earn a wage while developing their skills and knowledge needed to be able to pursue a career in the furniture, furnishings and interiors manufacturing industry.
A Furniture Making Operative would be expected to manufacture the various components needed to produce fitted kitchens, bathrooms or bedrooms. They measure, prepare and mark out materials and set up and operate machinery. Some will need to use computer numerically controlled (CNC) machinery and other technology involved in manufacturing furniture. They assemble, rectify, rework and repair furniture and understand finishing techniques.
In their daily work, an employee in this occupation interacts with a range of colleagues. These include other furniture making operatives, designers, production or manufacturing managers, quality technicians, production leaders and product developers. They usually report to a supervisor or shift team leader. They will be able to work with minimum supervision.
An employee in this occupation will be responsible for the quality, accuracy, and timely completion of their own work. They will be responsible for meeting production targets. They must work within the health, safety and environmental regulations and guidance, including use of appropriate protective clothing and equipment. All work must be completed in a safe and efficient manner as directed by supervisory staff. They are responsible for ensuring that they use resources efficiently. They recycle and reuse resources where possible, minimising waste and must include the safe disposal of waste.
Are there any entry requirements?
Must be a UK citizen, or have the right of abode in the UK, or is a citizen of a country that is within the EEA and have been ordinarily resident in the UK, the EU or the EEA continuously for the previous three years before the start of learning.
Candidates will have achieved a minimum of GCSE Grade 1 (G) or equivalent Level 1 in English and Mathematics. We also offer Functional Skills English and maths at Level 1 and Level 2 for those needing to gain these qualifications prior to enrolment.
Apprentices must be employed, normally for a minimum of 30 hours, in a role that suits the skills requirements of this apprenticeship. If you are not already employed, in this type of job role, you could search our apprenticeship vacancy page at:
www.darlington.gov.uk/jobs-and-careers/apprenticeships/apprenticeship-vacancies/
New applicants will be contacted by a vocational delivery tutor to determine suitability/ eligibility prior, give information and advice on the next steps.
Shortlisted applicants will be sent to the employer, to then follow their recruitment procedure. Unsuitable applicants will be signed posted to other areas of our service to develop transferable/ employability skills, with a view to ensuring they are suitable for other apprenticeship positions in the future.
What is the curriculum intent of this Apprenticeship?
The structure and delivery of the course curriculum will enable you to develop the skills, knowledge and behaviours to reflect the needs of local and regional employers, gain qualifications and be successful in this area.
The curriculum is planned and sequenced to enable learners with previous knowledge and experience to develop the new skills needed to progress to the next stage of their career, training, education or employment.
The curriculum is flexible and responsive to learner demands and can be tailored to suit individual needs arising from any current and dynamic issues affecting their role, which can be addressed during workshop sessions.
As an apprentice you will need to be able to demonstrate knowledge and practical skills at the end of your apprenticeship training programme and understand how this reflects the needs of the local, regional and national economy.
What will the Apprenticeship cover?
The Furniture Making Operative Level 2 Apprenticeship will develop the knowledge and understanding of:
- The furniture industry function and role of the operative. Responsibilities, limits of role and escalation procedures.
- Job specifications, technical drawings and technical information.
- Planning for furniture manufacturing activity, work organisation, resources, materials and time management.
- Safe systems of work including risk assessments.
- Awareness of health and safety regulations, standards, and guidance and impact on role.
- Environment and sustainability regulation, standards and guidance relevant to the occupation and the operative’s responsibilities.
- Preparation and maintenance of the work area.
- Workplace operating procedures. What they are and why they are important.
- Tools and equipment used in furniture manufacturing.
- Storage environment, for tools and equipment.
- Maintenance of tools and equipment including pre-checks, inspections and tool condition.
- Machinery used in furniture manufacturing.
- Maintenance of machinery for furniture manufacturing activity.
- Setting up machinery to perform furniture manufacturing operations.
- Types of materials used in furniture making.
- Jigs and templates. Purpose, condition and use.
- Measuring and marking out of materials.
- Furniture component manufacturing processes.
- Types of jointing techniques used in making furniture.
- Furniture assembly techniques.
- Types of furniture fittings and fixtures.
- Principles and techniques for finishing furniture surfaces, including spraying.
- Rectification, repair and rework techniques used on manufactured furniture.
- Methods for the handling and movement of products and components.
- Quality assurance processes.
- Methods of documenting work in progress for the furniture making activity.
- Continuous improvement techniques: lean manufacturing, six sigma, 5S and KAIZEN.
- Team working principles.
- Principles of equity, diversity, and inclusion in the workplace and the impact on their work.
- Verbal communication techniques. Giving and receiving information.
- Written communication techniques - electronic and paper. Industry terminology
- Information and digital technology: email, collaboration packages, databases, equipment digital interfaces, management information systems, word processing, work sharing platforms, GDPR, cyber security.
Develop Skills in:
- Read and interpret job specifications, technical drawings or information for furniture making activity.
- Plan furniture making activity.
- Prepare and maintain the work area.
- Apply safe systems of working including risk assessment.
- Follow health and safety regulations, standards, and guidance.
- Follow procedures in line with environmental and sustainability regulations, standards, and guidance. Segregate resources for reuse, recycling and disposal.
- Follow workplace operating procedures.
- Store tools and equipment.
- Select tools, equipment, and machinery for furniture making activity.
- Apply first line maintenance of, tools, equipment, and machinery.
- Set up and operate furniture making machinery.
- Identify and select materials used in furniture making.
- Apply preparation techniques to materials.
- Prepare and use jigs and templates used in the work activity.
- Measure and mark out materials, including measurement tool calibration checks.
- Manufacture furniture components including cutting and shaping.
- Apply jointing techniques to produce furniture components.
- Assemble and secure furniture components in position.
- Carry out rectification, repair and rework of manufactured furniture.
- Follow quality assurance processes.
- Pack and store components and products.
- Record furniture making activity information.
- Apply basic continuous improvement techniques.
- Apply team working principles.
- Apply escalation procedures in relation to faults or issues.
- Follow equity, diversity and inclusion rules.
- Communicate verbally with colleagues and supervisors.
- Communicate in writing with colleagues and supervisors.
- Use information technology and digital systems.
- Comply with GDPR and cyber security regulations and policies.
Develop and demonstrate the following behaviours:
- Put health and safety first.
- Take ownership of given work.
- Consider the impact on the environment when using resources and carrying out work.
- Team-focus to meet work goals.
- Support an inclusive workplace for example, respectful of different views.
- Seek learning and development opportunities.
On completion of the on-programme element of the apprenticeship you will enter gateway to the End Point Assessment, which is the final assessment. This will be conducted by an independent end point assessor who will grade the assessment.
End Point Assessment Methods
To trigger the End Point Assessment, you must have:
- Have proof of English & maths GCSE minimum grade 1/ G or equivalent level 1 qualification.
- Completed a showcase portfolio, demonstrating how you have met the knowledge, skills and behaviours.
The End Point Assessment consists of:
- Observation of Practice – 3hrs observed in the workplace (this includes Q&A).
- Professional discussion – 70 mins (underpinned with a portfolio of evidence).
This standard will be graded as Distinction, Pass or Fail.
What could I do when I have finished this Apprenticeship?
You may gain employment with your employer and / or work towards another Apprenticeship, depending on job role, such as Lean Product Operative L2 or Team Leader L3.
You will also be given information and guidance to continue onto other courses.
Where and when will I learn?
During the course you will be expected to attend one of our training centres, once a month to work towards the mandatory elements of the standard via the e-portfolio. The remaining days will be spent working with your employer gaining the skills, knowledge and behaviours required in preparation for End Point Assessment (EPA). English and maths are embedded into your training programme.
*Please note, Training can also take place via Teams and delivered anywhere in England.
This on-programme taught element will typically take 12 months, but this is based on a vocational initial assessment to determine prior learning in this area. The End Point Assessment will be completed within 3 months of completing the on-programme taught element.
This on-programme taught element will typically take 18 months, but this is based on a vocational initial assessment to determine prior learning in this area and may be reduced. The course duration is based on the apprentice working 30 hours per week but will be extended if the apprentice works less hours. The End Point Assessment will be completed within 3 months of completing the on-programme taught element.
How much will the Apprenticeship cost?
There are no fees for this apprenticeship.
What do I do next?
You can:
Or you can:
- Apply for this apprenticeship area [external link] to be entered into a 'pool of candidates'. When a relevant vacancy becomes available we will contact you.
- If you are already employed in this area and wish to join the apprenticeship training, or have identified an employer wishing to start you as an apprentice in this area, please contact us